Infrared Temperature Sensors
Our Compact Infrared Sensors Thermometer Series includes a wide range of noncontact pyrometers for industrial and OEM applications in temperatures ranging from -40 to 1650°C (-40 to 3002°F).
Request a quote today: sales@ptsheat.com
Raytek CI
Compact and easy to install, the Raytek CI noncontact infrared pyrometer measures temperatures ranging from 0° to 500°C (32°F to 932°F). Accessories are available for cooling and air-purg
Raytek CM Infrared Sensors
With temperature ranges from -20 to 500°C (-4 to 932°F), the Raytek CM is a rugged single-piece system with the flexibility to handle a variety of OEM and end-user manufacturing applications.
Raytek GP
The Raytek GP infrared pyrometers come with two types of rugged sensors: GPR and GPS. They both provide standard or close focus optics and target temperature from minus 18° to 538°C (0° to 1000°)
Raytek MI3
With an extended temperature range of -40 to 1800°C (-40 to 3272°F) and multi-sensor design, the MI3 Series represents a new generation of performance and innovation in noncontact temperature monitoring for OEM applications and manufacturing processes. Intrinsically safe MI3 models are specifically designed for use in explosive atmospheres.
Metal Processing
Monitor temperatures in all steps of the metallurgical process with infrared thermometers.
Building & Construction Materials
Verify temperatures in cement, construction materials, and architectural glass manufacturing.
Glass Processing
Monitor temperatures in Melt Furnace, Flat Glass, Bottles and Containers, and Glass Fiber production.
Packaging, Paper & Converting
Use IR sensors in automation applications including packaging, printing and converting.
Plastic Processing
Measure temperatures of extrusion, thermoforming and coating to ensure top product quality.
Solar Industry
Monitor temperature at every step of your process to improve productivity and product quality.
Maintenance
Reduce maintenance costs and improve safety with non contact IR temperature systems.
Other Applications
Use IR sensors in fire detection, tobacco drying, food, automotive, electrical, plant and facilities monitoring applications.
Blow Molding is a Perfect application for infrared sensors
IRt/c’s measure the temperature of blow molding preforms while they move and rotate.
General Information
In the process of making PET bottles (polyethylene terephthalate), there is a fine line where the high output per bottle blowing machinery and the requested quality of the bottle comes together. Taking into account that such machines must be able to produce a broad range of sizes and shapes and produce various quality bottles, it’s obvious that many variables must be kept under control during the process. One of the key parameters to control is the temperature.
How does this work?
The bottle blowing station machine’s infeed starwheel picks up the preforms and transfers them to the preform conveyor belt. Then, while rotating continually, they run through a system intended to uniformly heat up the preform. When a set temperature is reached, the preform is moved to the blow molding section of the machine, where it is molded in the desired shape by applying pressurized air. If the temperature of the preform is not uniform, or has not reached or has exceeded the desired value, the end product will have defects: holes in the bottle if the temperature was too high, not completely extended bottles if the temperature was too low, or variances in the thickness of the bottle if the temperature was not uniform (or combinations of these three). These bottles have to be discarded and this reduces the yield of the machine and increases the waste.
To avoid defects or deformities in the end product, it is essential that the temperature of the preform is monitored and controlled in the heating step prior to molding. This monitoring enables a temperature variance comparison and (if necessary) allows for automatic correction of the heating parameters, making sure the optimum quality and speed are obtained.
The Optimal Solution
Since the preforms are moving and rotating, their temperature can only be measured by the use of a non-contact, infrared temperature sensor. As small temperature variations during the heating can result in deformities of the end product, it is essential to employ a sensor with high accuracy and speed. The ambient temperature close to the heater can vary significantly and the sensor must be able to deal with these variations without generating measurement errors.
Finally, blow molding machines generally operate 24/7 to optimize yield and profit, so a sensor should be employed that will not create any downtime or require regular maintenance or re-calibration.
Why PTSHEAT IR Non-Contact Sensors?
PTSHEAT’s non-contact IRt/c sensors are the most accurate sensors available and are ideally suited to measure moving and rotating objects. The IRt/c’s patented Ambient Temperature Compensation methodology ensures optimal performance in varying ambient temperatures. Further advantages of the IRt/c are:
– Self-powered, no service or calibration needed
– Provides response times ranging from 25 to 100 milliseconds that won’t slow down the process
– Repeatability error of 0.01°C (0.02°F) – consistent readings now and in 10 years time
– Interchangeability error of +-1% – results will remain the same between different machines.
Commercial Advantages
– Optimized process due to very accurate and fast readings, faster production
– Better yield, less scrap, and waste
– Better quality of the end product
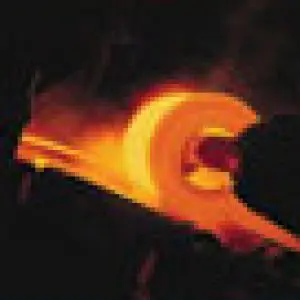
Metal Processing
Monitor temperatures in all steps of the metallurgical process with infrared thermometers.
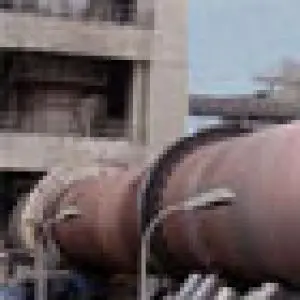
Building & Construction Materials
Verify temperatures in cement, construction materials, and architectural glass manufacturing.