RTD’s Resistance Temperature Detectors
PTSHEAT sales engineers can design exact fit PT100 RTD’s to replace your original equipment and for new applications. We guarantee our parts! We will supply proper form, fit, function sensors every time. Please allow us the opportunity to work with you on your RTD’s needs!
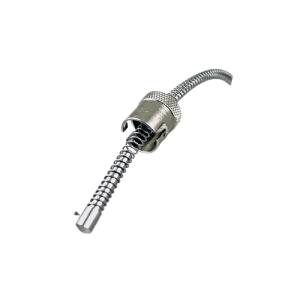
Bayonet Style sensors

MeltBolt sensors
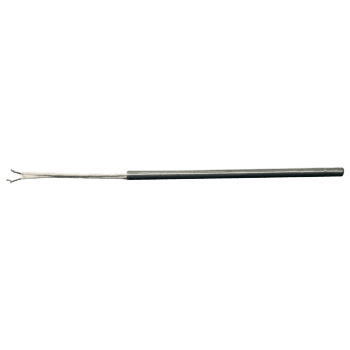
Tube and Wire Assemblies
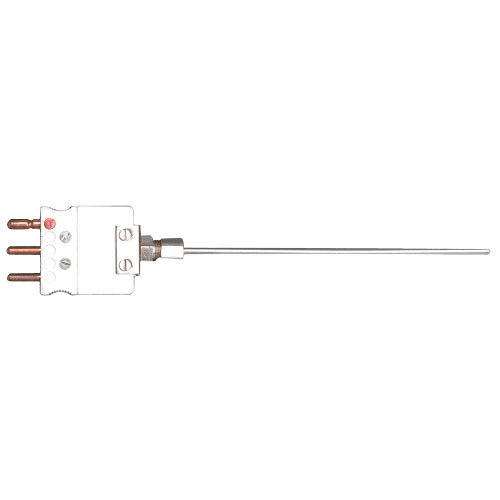
Style AC / R2 Plug or Jack Termination
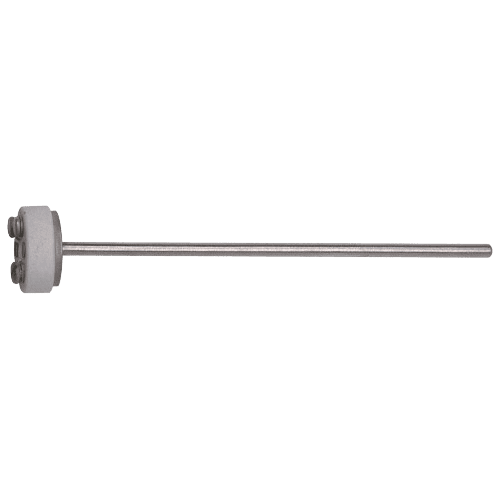
Wafer Head Assembly

Sensors with Fittings for heads and through wall
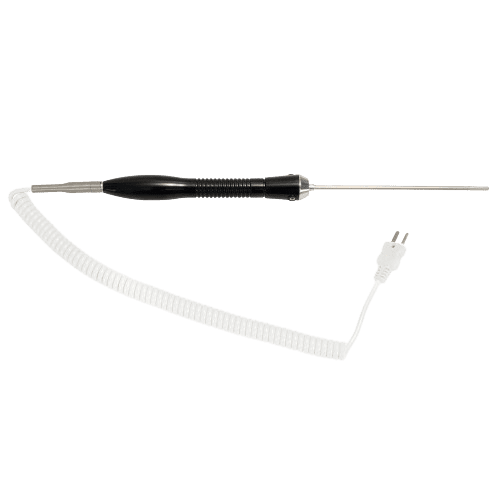
Hand Held Probe for process testing / measurement
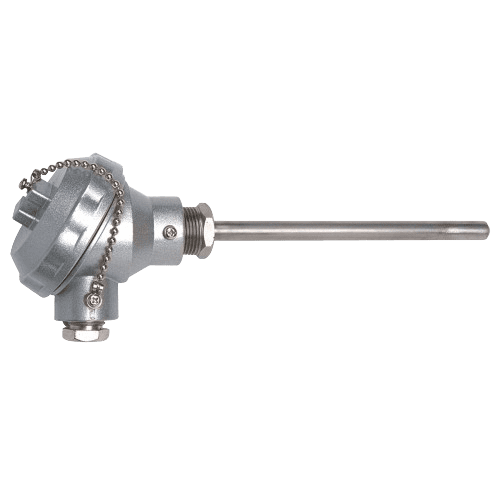
Connection Head
RTD’s
Resistance Temperature Detectors (RTD’s) are temperature sensing devices consisting of a wire coil or deposited film of pure metal, usually platinum. The element’s resistance increases with temperature in a known and repeatable manner. RTD’s exhibit excellent accuracy over a wide temperature range, –200 to 650°C (–328 to 1202°F).
———— RTD’s offer ————
Standardization: RTD’s are manufactured to industry standard curves, usually 100 ohm platinum to IEC 751, which makes them very interchangeable.
Stability and repeatability: The platinum RTD is the primary interpolation instrument used by the National Institute of Standards and Technology from –260 degrees Celsius to 630 degrees Celsius. Precision RTD’s can be manufactured with a stability of 0.0025 degrees Celsius per year. However, most industrial models drift less than 0.1 degrees Celsius per year.
———— RTD’s offer ————
Linearity: The platinum RTD produces a more linear curve than thermocouples or thermistors. The RTD’s non-linearities can be corrected through proper design of resistive bridge networks.
Sensitivity: The voltage drop across an RTD provides a much larger output than a thermocouple. Since thermistors have a higher resistance than RTD’s, the measuring current through them may be so low as to limit self-heating, making their voltage drop less than that of an RTD.
System Cost: RTD’s usually offer a lower system cost than do thermocouples as they use ordinary copper extension leads and require no cold junction compensation.
Specifications and Compliances?
All of Phoenix Thermal Supply’s RTD’s comply with the following specifications:
IEC publication 751 issued by the International Electrotechnical Commission (dated 1983).
This is the widest international scope of any RTD standard. This publication sets the tolerance for platinum RTD’s with a value of 100 ohms at 0°C with a temperature coefficient of resistance (TCR) of 0.00385 ohms/ohm/°C in one of two classes:
Class A: Plus or minus 0.06% at 0°C
Class B: Plus or minus 0.12% at 0°C
All PTSHEAT RTD’s meet class B; class A is optional.
DIN 43760 issued by Deutsches Institute fur Normung (Germany), dated 1987. The platinum resistance curves are now covered under DIN IEC 751.
JIS 1604-1989 issued by the Japanese Standards Association (dated 1989).
The Platinum resistance curves are in accordance with IEC 751 but there is also a provision for TCR 0.003916 ohms/ohm/°C which can be supplied in most of PTSHEAT’s standard designs on special request.
BS 1904-1984 issued by the British Standard Institute (dated 1984). This specification is identical to IEC 751
What is Temperature Coefficient of Resistance (TCR)?
Temperature coefficient differentiates between resistance/temperature curves of RTD’s. It is also called ALPHA and may be specified in various ways by different manufacturers. Here TCR is the RTD’s resistance change from 0 to 100°C, divided by the resistance at 0°C, divided by 100°C:
Example: A platinum RTD measuring 100 Ω’s at 0°C and 138.5 Ω’s at 100°C has TCR 0.00385 Ω/Ω/°C
Stated another way, TCR is the average resistance increase per degree of a hypothetical RTD measuring 1 ohm at 0°C.
The most common use of TCR is to distinguish between curves for platinum, which is available with TCR’s ranging from 0.00375 to 0.003927. The highest TCR indicates the highest purity platinum, and is mandated by ITS-90 for standard platinum thermometers.
There are no technical advantages of one TCR versus another in practical industrial applications. 0.00385 platinum is the most popular worldwide standard and is available in both wire-wound and thin-film elements.
In most cases, all you need to know about TCR is that it must be properly matched when replacing RTD’s or connecting them to instruments.
Interchangeability and Repeatability
Interchangeability and accuracy are commonly cited as the RTD’s most distinguishing attributes. Because of the tight tolerances of the Class A and Class B, RTD’s are quite interchangeable. Their accuracy is also very good because of the RTD’s repeatability over the standard temperature scale from –260°C to 630°C. Ordinary industrial RTD’s tend to show a drift of less than 0.1°C per year in normal use.
Because RTD’s are exactly what the name implies (Resistance Temperature Detector), a resistance type sensor, any resistance introduced by the addition of extension wires between the RTD and the control or measuring instrument will add to the readings. This added resistance is not constant since the extension wires, usually copper, change their resistance values with changing ambient temperature. Extension wire errors can be significant, particularly with small gauge wires or elements with low sensitivity. Fortunately most of these errors may be nearly canceled by using a three wire system.
The majority of RTD’s in today’s industry are 3- or 4-wire systems; the 2-wire lead system is the least efficient unless the leads are heavy gauge, very short, or both.
In 3- or 4-wire circuits, common leads, connected to the same end of the RTD element, are the same color.
Applications:
- Food Processing Equipment
- De-Icing
- Platens
- Molds and Dies
- Plastic Injection Molding Equipment
- Extrusion Equipment
- Ovens
- Industrial Heat Treating
- Liquid Temperature Control
- Medical Equipment
- Process Temperature Measurement